Infrared Tunnel Oven (Forced Convection Oven)
Developed by C SAIL, this tunnel infrared oven is designed with hot air drying function based on infrared drying, thus obtaining a more uniform temperature and smooth discharge of volatile gasses, which results in a high drying efficiency.
This tunnel infrared oven with hot air is widely used in sophisticated product industry, like TP, LCD, COVERLENS, OGS, light guide plate, film, as well as fields like curing of touch panel silver paste, film, CG printing ink, mirror like silver, IR oil, and more.
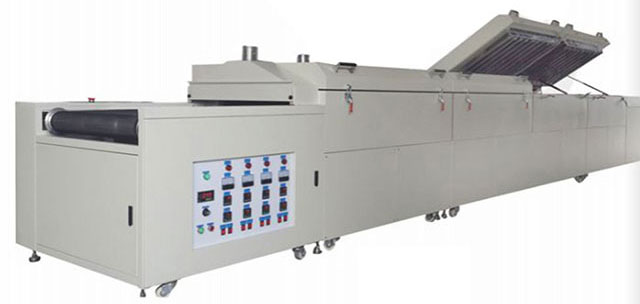
Display of different types of tunnel infrared oven
SCO-IR-8-4 tunnel infrared oven
Model | |
Power | 380V |
Heating method | IR+ hot air |
Length of Feeding Part (mm) | 1200 |
Length of Heating Part (mm) | 6000 |
Length of Cooling Part (mm) | 1000 |
Length of Discharging Part (mm) | 800 |
Height of Feeding inlet and Discharging Outlet (mm) | 50 |
Width of Wire Mesh Conveyor Belt (mm) | Teflon 800 |
Temperature Range | Room Temperature-200℃ |
Temperature uniformity (±%) | ±2% |
Send an Inquiry |
SCO-IR-9-4 tunnel infrared oven
Model | |
Power | 380V |
Heating method | IR+ hot air |
Length of Feeding Part (mm) | 1300 |
Length of Heating Part (mm) | 4700 |
Length of Cooling Part (mm) | 1500 |
Length of Discharging Part (mm) | 900 |
Height of Feeding inlet and Discharging Outlet (mm) | 50 |
Width of Wire Mesh Conveyor Belt (mm) | Teflon 900 |
Temperature Range | Room Temperature-200℃ |
Temperature uniformity (±%) | ±2% |
Send an Inquiry |
SCO-IR-10-3 tunnel infrared oven
Model | |
Power | 380V |
Heating method | IR+ hot air |
Length of Feeding Part (mm) | 500 |
Length of Heating Part (mm) | 5000 |
Length of Cooling Part (mm) | |
Length of Discharging Part (mm) | 500 |
Height of Feeding inlet and Discharging Outlet (mm) | 200 |
Width of Wire Mesh Conveyor Belt (mm) | Teflon 1000 |
Temperature Range | Room Temperature-200℃ |
Temperature uniformity (±%) | ±2% |
Send an Inquiry |
SCO-IR-10-4 tunnel infrared oven
Model | |
Power | 380V |
Heating method | IR+ hot air |
Length of Feeding Part (mm) | 1100 |
Length of Heating Part (mm) | 6000 |
Length of Cooling Part (mm) | 1100 |
Length of Discharging Part (mm) | 1000 |
Height of Feeding inlet and Discharging Outlet (mm) | 50 |
Width of Wire Mesh Conveyor Belt (mm) | Teflon 1000 |
Temperature Range | Room Temperature-200℃ |
Temperature uniformity (±%) | ±2% |
Send an Inquiry |
SCO-IR-10-6 tunnel infrared oven
Model | |
Power | 380V |
Heating method | IR+ hot air |
Length of Feeding Part (mm) | 1000 |
Length of Heating Part (mm) | 10000 |
Length of Cooling Part (mm) | 1000 |
Length of Discharging Part (mm) | 1000 |
Height of Feeding inlet and Discharging Outlet (mm) | 50 |
Width of Wire Mesh Conveyor Belt (mm) | Stainless Steel Chain Mesh 1000 |
Temperature Range | Room Temperature-200℃ |
Temperature uniformity (±%) | ±2% |
Send an Inquiry |
SCO-IR-8-3 tunnel infrared oven
Model | |
Power | 380V |
Heating method | IR+ hot air |
Length of Feeding Part (mm) | 800 |
Length of Heating Part (mm) | 3500 (including 500mm preheat section) |
Length of Cooling Part (mm) | 600 |
Length of Discharging Part (mm) | 300 |
Height of Feeding inlet and Discharging Outlet (mm) | 350 |
Width of Wire Mesh Conveyor Belt (mm) | Stainless Steel Chain Panel 800 |
Temperature Range | Room Temperature-200℃ |
Temperature uniformity (±%) | ±2% |
Send an Inquiry |
Features:
- The tunnel infrared oven with hot air will penetrate any product for simultaneous interior and exterior drying. In doing so, products are heated in a uniform manner and product quality is guaranteed.
- High drying efficiency: a traditional drying oven takes several hours to dry, whereas a tunnel infrared oven with hot air takes less than an hour. By shortening the heating period, energy and manufacturing costs are both reduced.
- Reduced failure rate; synchronous control of the heating device and production line, product deformation and product blistering are reduced due to suspended production.
- This tunnel infrared oven can be divided into 3 parts, and the temperature of each part can be set independently, leading to a high applicability with different coatings.
- Easy temperature control, fast heating and high security
- Low thermal inertia, no need for turbine warming up, energy saving performance